Spline hydraulic rotary actuators have been vital in various industries for their reliable and powerful performance. Looking ahead, the future of these actuators holds several exciting possibilities.
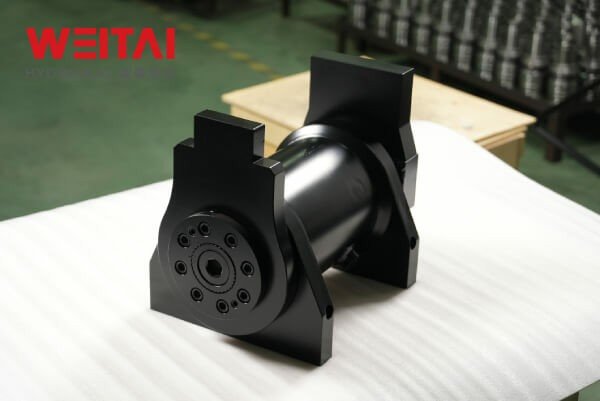
Advantages of Spline Hydraulic Rotary Actuators
High Torque Output: Spline hydraulic rotary actuators can generate significant torque, making them suitable for heavy-duty applications. For instance, they are commonly used in large-scale industrial machinery for tasks requiring substantial rotational force, such as metal forging presses.
Precise Positioning: These actuators offer precise control over rotational movement, allowing for accurate positioning in operations. This is crucial in applications like robotics and CNC machines where even the slightest deviation can affect the output quality.
Smooth and Continuous Operation: They provide a smooth and consistent rotational motion without jerks or fluctuations. This ensures a seamless workflow and reduces wear and tear on connected components. An example is in packaging machinery where a smooth operation is essential to avoid damaging the packaged items.
Durability and Long-Service Life: Built with robust materials and designed to withstand harsh operating conditions, spline hydraulic rotary actuators have a long lifespan. They can handle high loads and frequent use without significant degradation in performance.
Wide Operating Temperature Range: They can function effectively in a wide range of temperatures, making them suitable for use in various environments, from extremely cold to hot industrial settings.
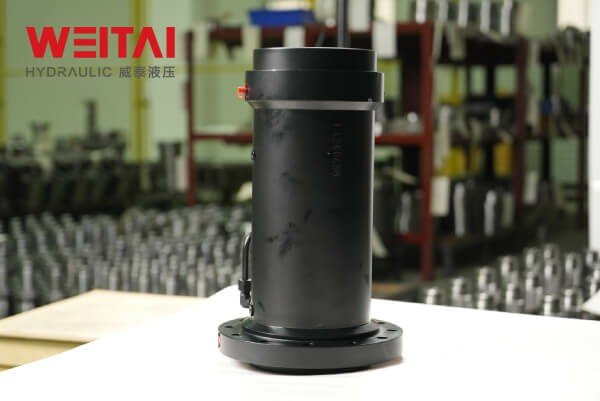
Limitations of Spline Hydraulic Rotary Actuators
Maintenance Requirements: Hydraulic systems, including spline rotary actuators, often require regular maintenance to ensure proper functioning. This includes checking for leaks, changing hydraulic fluid, and inspecting seals and components. The maintenance process can be time-consuming and costly.
Potential for Leakage: Hydraulic fluid leaks are a common issue, which can not only lead to performance degradation but also pose environmental hazards. In some cases, leaks can cause damage to the surrounding equipment and workspace.
Complexity of the System: The hydraulic system associated with these actuators is relatively complex, requiring skilled technicians for installation, troubleshooting, and repair. This complexity can increase the initial setup cost and the difficulty of maintenance.
Energy Consumption: Hydraulic systems typically consume more energy compared to some other actuation methods. This can have an impact on overall operational costs, especially in applications where energy efficiency is a key concern.
Size and Weight: Spline hydraulic rotary actuators can be bulky and heavy, which may limit their use in applications where space and weight are critical factors.
Future Trends of Spline Hydraulic Rotary Actuators
One major trend is the continued improvement in precision and control. With advancements in sensor technology and feedback systems, spline hydraulic rotary actuators will be able to achieve even more accurate and fine-tuned rotational movements. This will be crucial in applications such as aerospace, where precise maneuvering is essential for the success of missions.
Energy efficiency is another area where we can expect significant developments. As the focus on sustainable practices grows, efforts will be made to reduce the energy consumption of these actuators. This might involve the use of more efficient hydraulic fluids, improved sealing to minimize losses, and the integration of energy recovery systems.
The miniaturization of spline hydraulic rotary actuators is also on the horizon. This will open up new opportunities in the field of micro-robotics and medical devices, where small but powerful actuators are in high demand. For example, in minimally invasive surgical tools, compact and precise actuators could enable more complex and delicate procedures.
In the context of Industry 4.0 and the increasing digitization of manufacturing processes, these actuators will likely become more intelligent and connected. They will be integrated with Internet of Things (IoT) platforms, allowing for real-time monitoring of performance, predictive maintenance, and seamless communication with other components of the production line.
Furthermore, materials science advancements will lead to the development of stronger and lighter components for the actuators, enhancing their durability and portability. This could have implications in the automotive industry, where lighter and more efficient actuators could contribute to improved vehicle performance and fuel economy.
Finally, research and development in alternative hydraulic fluids that are environmentally friendly and have better performance characteristics will shape the future of spline hydraulic rotary actuators. This will help industries meet stricter environmental regulations while maintaining or improving the actuators’ functionality.
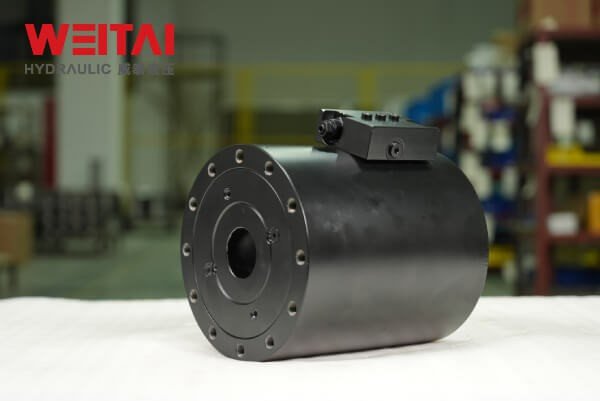
Conclusion
Overall, the future of spline hydraulic rotary actuators looks promising, with continuous innovation set to drive their performance, efficiency, and application scope to new heights.