A helical hydraulic actuator is a type of mechanical device that converts hydraulic pressure into rotational or linear motion.
It typically consists of a helical screw or thread within a cylinder. When hydraulic fluid is pumped into the actuator at a specific pressure, it forces the helical component to move along its axis, resulting in rotational or linear displacement.
The helical design provides several advantages. It allows for more efficient force transmission and higher torque output compared to some other actuator designs. This makes helical hydraulic actuators suitable for heavy-duty applications that require significant power and precise movement control.
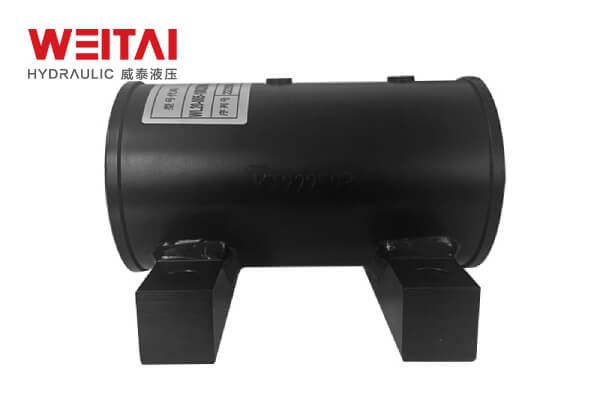
Pros of Helical Hydraulic Actuator Compared to Traditional Actuator
Higher Efficiency: Helical hydraulic actuators frequently showcase enhanced energy conversion efficiency. This means they can achieve the same amount of work with less input power. Consider a construction vehicle’s lifting mechanism; a helical hydraulic actuator could consume significantly less fuel to generate the necessary force to lift heavy loads. The improved efficiency not only reduces operational costs but also contributes to a more environmentally friendly operation.
Compact Design: The unique helical configuration enables a more space-efficient layout. In modern engineering, where space is often at a premium, this is a considerable advantage. For instance, in advanced robotics or compact automotive systems, the ability to fit the actuator into tight spaces without sacrificing performance is crucial. It allows for more streamlined and integrated designs, maximizing the available space for other components.
Smooth and Precise Movement: One of the standout features of helical hydraulic actuators is their ability to provide exceptionally smooth and precise rotational or linear motion. This level of accuracy is indispensable in applications such as medical devices, particularly surgical robots. The precise control ensures that delicate and complex surgical procedures can be carried out with minimal error and maximum safety for the patient.
Higher Torque Output: The helical design often allows for the generation of greater torque compared to traditional actuators. This makes them the preferred choice in heavy-duty applications where immense force is required. Picture a large industrial press used in manufacturing; a helical hydraulic actuator can exert the necessary pressure to shape and form materials with ease, whereas a traditional actuator might struggle to meet the demanding force requirements.
Durability and Longevity: Due to their robust construction and efficient force distribution, helical hydraulic actuators typically have an extended service life. In continuous-operation industrial environments, where downtime is costly, their durability ensures reliable performance over long periods. This reduces the frequency of maintenance and replacements, translating into significant savings in both time and resources.
Cons of Helical Hydraulic Actuator Compared to Traditional Actuator
Complexity in Maintenance: The helical design and the intricate nature of the hydraulic components introduce a higher level of complexity when it comes to maintenance. Specialized knowledge, tools, and diagnostic equipment are often required. In contrast, a simple mechanical actuator might be easier to troubleshoot and repair. For example, identifying and addressing a leak in a helical hydraulic actuator’s complex sealing system can be a time-consuming and challenging task.
Leakage Risk: Hydraulic systems, including those with helical actuators, are notorious for their potential fluid leakage. Even a minor leak can have significant consequences. It not only leads to performance degradation as the actuator loses pressure and force but also poses environmental hazards as the leaked fluid can contaminate the surrounding area. Traditional actuators that do not rely on hydraulics, such as some electric or pneumatic alternatives, typically have a lower risk of leakage.
Cost of Initial Installation: The initial setup cost of helical hydraulic actuators can be considerably higher than that of traditional actuators. This encompasses the expense of the actuator itself, which may be more complex and sophisticated in design, as well as the associated hydraulic system components like pumps, valves, and tubing. Additionally, the installation process often requires skilled technicians and specialized equipment, further adding to the overall cost.
Sensitivity to Contamination: The hydraulic fluid in helical actuators is susceptible to contamination from various sources such as dirt, moisture, and debris. Even small amounts of contamination can adversely affect the performance and longevity of the actuator. Maintaining the purity of the fluid through regular filtering and monitoring is essential but adds to the maintenance burden and cost.
Temperature Sensitivity: Extreme temperatures can have a more pronounced impact on the performance and reliability of the hydraulic fluid and components in helical actuators compared to certain traditional actuator types. In very cold conditions, the fluid might thicken, reducing flow and affecting the actuator’s speed and force. In hot environments, the fluid can break down more quickly, increasing the risk of component wear and failure. Special cooling or heating measures might be necessary in environments with extreme temperature variations to ensure optimal performance.
The performance of a helical hydraulic actuator depends on factors such as the quality of the hydraulic fluid, the sealing of the components to prevent leaks, and the design and manufacturing precision of the helical mechanism.
Conclusion
Overall, helical hydraulic actuators are essential components in various industries where powerful and controlled motion is necessary for the efficient operation of equipment and systems.