The hydraulic track drive is the driving force behind the mobility of heavy machinery, such as excavators, skid steers, and tracked loaders. These components bear significant stress from tough terrains, heavy loads, and long operational hours. Over time, wear and tear are inevitable, leading to performance issues. When your hydraulic track drive starts showing signs of failure, you may face a crucial decision: Should you fix it or invest in a new one? In this post, we’ll explore the key factors to help you decide when to repair your track drive and when it’s time for a replacement.
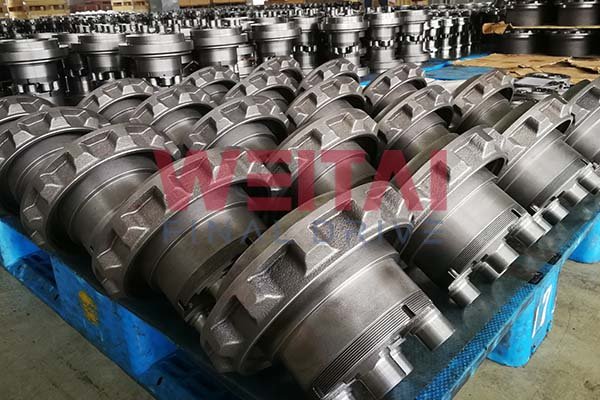
1. Assess the Severity of the Issue of the Hydraulic Track Drive
The first step in deciding whether to fix or replace your hydraulic track drive is to assess the severity of the problem. Not all issues require a complete replacement; some can be resolved with repairs or part replacements.
Common repairable issues:
- Leaking seals or gaskets: Minor hydraulic fluid leaks due to worn seals or gaskets can often be fixed with seal replacements, which is relatively inexpensive and quick.
- Clogged hydraulic filters: If your track drive is losing power or running sluggishly, clogged filters may be the culprit. Replacing these filters can restore normal performance.
- Minor component wear: Bearings, sprockets, or small internal parts that show signs of wear can be replaced without replacing the entire unit.
However, when the damage extends to more critical components or the entire system, a full replacement may be necessary.
Serious issues requiring replacement:
- Catastrophic internal failure: If internal gears, shafts, or hydraulic motors are severely damaged, the cost of rebuilding the entire unit may exceed the cost of a new track drive.
- Frequent breakdowns: If your hydraulic track drive frequently breaks down despite regular repairs, this is a sign that the system is nearing the end of its service life and should be replaced to avoid constant downtime.
2. Consider the Age of the Hydraulic Track Drive
The age of your hydraulic track drive plays a significant role in the fix-or-replace decision. Like any mechanical component, track drives have a finite lifespan, and repairing an older drive may not always be the most cost-effective option.
Key considerations:
- Lifespan: Track drives generally last for several thousand operating hours, depending on usage and maintenance. If your drive is nearing or has exceeded its expected lifespan, investing in a new unit is often the better option.
- Obsolete parts: As track drives age, finding replacement parts can become more difficult or expensive, especially if the model is no longer manufactured. In such cases, a full replacement may be more practical.
If your track drive is relatively new or has significant life left, repairing it can extend its useful life and delay the need for a replacement.
3. Evaluate Repair Costs vs. Replacement Costs
One of the most important factors to consider is the cost of repairing the track drive compared to replacing it. In some cases, repairs may be a short-term fix that could end up costing more in the long run.
Key considerations:
- Cost of repairs: Add up the total cost of repairs, including labor, parts, and downtime. If the cost of repairs is more than 50% of the cost of a new track drive, it may be more economical to invest in a replacement.
- Cost of downtime: If your equipment is frequently out of service due to ongoing track drive issues, the lost productivity and revenue can quickly add up. A new, reliable track drive can reduce downtime and improve efficiency.
For minor issues, repairing your hydraulic track drive is often the most cost-effective solution. However, if repairs are costly and frequent, replacement may save you money in the long run.
4. Analyze Performance and Efficiency
A declining hydraulic track drive can negatively impact your machine’s overall performance and efficiency. If your equipment is struggling to maintain power, speed, or control, it may be time to consider a replacement.
Key considerations:
- Reduced power: Track drives losing hydraulic power can cause sluggish movement or difficulty traversing tough terrain. Replacing the unit can restore full operational capacity.
- Increased fuel consumption: An inefficient track drive can cause your equipment to work harder, leading to higher fuel consumption. Newer track drives often come with improved efficiency features that save on fuel costs.
- Operational noise: Excessive noise during operation could indicate internal damage. While some minor issues can be fixed, a noisy or vibrating track drive may signal the need for a complete replacement.
Upgrading to a new track drive can improve performance and extend the overall efficiency of your machine, leading to smoother operation and reduced operational costs.
5. Maintenance History of the Hydraulic Track Drive
The maintenance history of your hydraulic track drive is another important factor to consider. Well-maintained track drives tend to have fewer issues and can often be repaired, while poorly maintained units may have deeper, hidden problems.
Key considerations:
- Regular maintenance: If your track drive has been regularly serviced and maintained, repairs can be an effective way to extend its life. Seals, filters, and other consumable parts are easy to replace when regularly checked.
- Neglected maintenance: If your track drive has missed multiple maintenance cycles or has been running with dirty hydraulic fluid, the internal damage may be significant. In this case, replacement is usually the better option.
A well-maintained hydraulic track drive is more likely to benefit from repairs, whereas neglected systems often require a full replacement to restore functionality.
6. Technological Advancements
Hydraulic track drives have evolved over the years, with newer models offering improvements in efficiency, durability, and ease of maintenance. If your equipment is using an older track drive model, replacing it with a newer one can provide significant operational benefits.
Key advancements to consider:
- Improved efficiency: Newer track drives are often more fuel-efficient, reducing operational costs.
- Enhanced durability: Modern materials and manufacturing techniques can extend the lifespan of newer track drives, minimizing the risk of frequent breakdowns.
- Easier maintenance: Many new track drives feature easier access to internal components, reducing the time and cost required for repairs and maintenance.
If you’re dealing with an older hydraulic track drive, upgrading to a new model could provide better long-term value, even if the current one is still operational.
Conclusion
Deciding whether to fix or replace your hydraulic track drive depends on a variety of factors, including the severity of the issue, the age of the track drive, repair costs, and the performance of your equipment. Minor issues with newer track drives can often be addressed through repairs, while older or severely damaged units may require full replacement to avoid ongoing costs and downtime.
Ultimately, investing in a new hydraulic track drive may provide the best long-term value, offering improved efficiency, performance, and durability for your heavy equipment. However, if repairs can restore functionality at a lower cost, they can be a viable solution for extending the life of your existing track drive.
By carefully assessing these factors, you can make an informed decision that keeps your equipment running smoothly and efficiently, whether through repairs or a new hydraulic track drive.