When your application requires smooth, high-torque rotational motion in a compact form, a helical hydraulic rotary actuator can be an ideal choice. These actuators are known for their ability to convert linear motion into rotary motion using a helical screw mechanism, offering powerful performance in confined spaces. However, choosing the right helical hydraulic rotary actuator involves several key factors that ensure optimal performance and longevity. In this blog post, we’ll explore the most important aspects to consider when selecting one for your system.
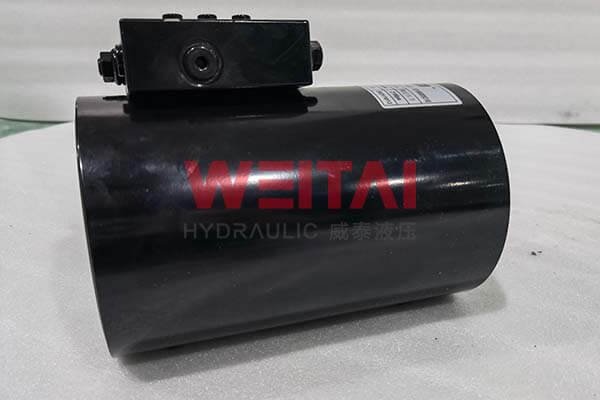
1. Understand Your Torque Requirements
Helical hydraulic rotary actuators are often selected for their high torque output in demanding applications. The first step in making the right choice is to determine your required torque. Consider the load you’ll be moving and the forces involved. Actuators come with different torque ratings, so ensuring you select one that can handle your application is crucial.
Torque requirements can vary greatly between different systems, such as:
Heavy-Duty Industrial Machines (requiring high torque)
Automated Production Lines (requiring moderate torque)
Small-Scale Equipment (requiring low to medium torque)
Make sure to calculate both the starting and operating torque to match your application’s demands.
2. Define the Range of Rotation
Helical hydraulic rotary actuators offer precise control over rotational motion, but it’s important to choose an actuator with the appropriate range of rotation. These actuators are typically available in several rotation ranges, such as:
90 degrees
180 degrees
270 degrees
360 degrees
Determine the exact degree of rotation your application requires. For example, a 180-degree actuator would be suitable for applications where half-turn motion is needed, while full 360-degree rotation may be necessary for applications requiring continuous movement.
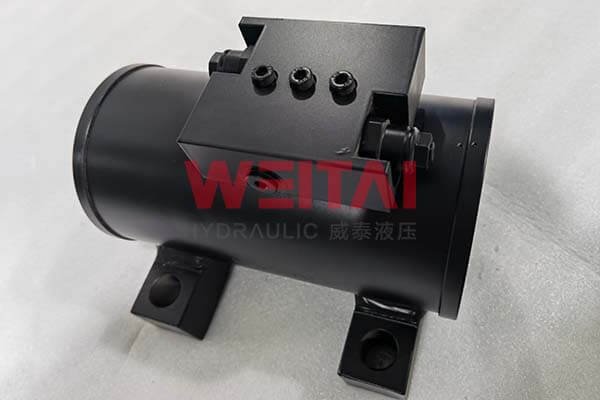
3. Assess Pressure and Flow Rate Requirements
Hydraulic systems rely on fluid pressure and flow rates to generate motion. Therefore, understanding your hydraulic pressure and flow rate specifications is critical for selecting the right actuator. Most helical hydraulic actuators are designed to handle high-pressure systems, but they come with different pressure ratings, so ensure the actuator can handle your system’s operating pressure.
Additionally, consider the flow rate required to achieve the desired rotational speed. A higher flow rate typically leads to faster rotation, but this must be balanced with the system’s capacity to provide the necessary hydraulic fluid without causing undue strain.
4. Consider the Operating Environment
Your actuator’s operating environment can significantly impact its performance and longevity. Helical hydraulic rotary actuators are often used in harsh conditions, so it’s essential to consider the following environmental factors:
Temperature: Extreme temperatures can affect the hydraulic fluid and actuator components. Ensure that the actuator is rated for the specific temperature range in your environment.
Corrosion Resistance: If the actuator will be exposed to corrosive substances or harsh chemicals (common in industries like oil & gas, marine, or mining), select a model with corrosion-resistant materials such as stainless steel or protective coatings.
Contamination and Debris: Sealed actuators can prevent dust, dirt, or moisture from entering and damaging internal components. Choose an actuator with the appropriate Ingress Protection (IP) rating for your operating conditions.
5. Mounting and Space Constraints
One of the benefits of helical hydraulic rotary actuators is their compact design, making them suitable for space-constrained applications. However, you still need to account for the physical dimensions of the actuator and ensure that it can be properly mounted in your system.
Axial and Radial Mounting: Depending on your application, you may need an actuator that supports either axial or radial mounting configurations. Be sure to check the actuator’s mounting specifications and alignment requirements to avoid installation issues.
Compactness: If your application involves tight spaces, consider the footprint of the actuator. Helical actuators generally offer high torque in a smaller package compared to other types of actuators, making them a great choice when space is limited.
6. Maintenance and Durability of the Helical Hydraulic Rotary Actuator
Hydraulic actuators often require regular maintenance to ensure longevity and optimal performance. When choosing a helical hydraulic rotary actuator, consider its maintenance requirements:
Sealing and Leakage Prevention: Well-sealed actuators minimize the risk of hydraulic fluid leakage, reducing the need for frequent maintenance.
Wear Resistance: Components that experience continuous motion, such as the helical screw, should be constructed from durable, wear-resistant materials to extend the life of the actuator.
Serviceability: Look for actuators that are easy to service and maintain. Actuators designed for quick access to internal components can significantly reduce downtime and labor costs.
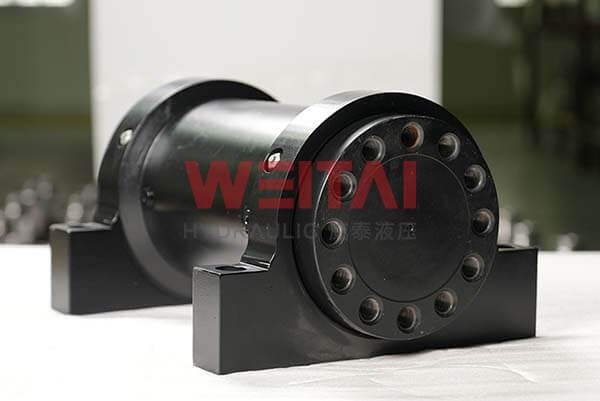
7. Control System Compatibility
Ensure that your selected actuator is compatible with your existing control system. Many hydraulic actuators rely on precise control systems to manage speed, torque, and position. Verify that your actuator can integrate with any feedback mechanisms, sensors, or hydraulic valves required for your application.
Position Feedback: If your system requires precise positioning, consider adding sensors like rotary encoders or position transducers to monitor and control the actuator’s position.
8. Cost Considerations
Finally, your budget will play a role in selecting the right actuator. While helical hydraulic rotary actuators can be an investment, consider the long-term savings from reduced maintenance, increased durability, and high efficiency. The upfront cost should be weighed against the benefits of improved performance, reliability, and system longevity.
Conclusion
Choosing the right helical hydraulic rotary actuator involves balancing your torque requirements, rotational range, hydraulic system specifications, and environmental factors. By carefully evaluating these criteria and considering factors like mounting, maintenance, and control system compatibility, you can make an informed decision that ensures optimal performance for your application.
Don’t hesitate to consult with a helical hydraulic rotary actuator manufacturer or experts if you’re unsure about your specific requirements. The right choice can enhance your system’s efficiency, extend equipment life, and save you time and money in the long run.