In the world of underground mining and tunneling, roadheaders are essential machines that make the excavation of rock and soil possible. These powerful machines rely on advanced hydraulic systems to perform their cutting, tunneling, and maneuvering tasks with precision and efficiency. However, the standard hydraulic solutions often need to be customized to meet the unique demands of each project. In this blog post, we explore how custom mobile hydraulic solution is transforming modern roadheader performance and what this means for industries that rely on these machines.
The Role of Hydraulics in Roadheaders
Hydraulics are the lifeblood of roadheader machines, providing the force needed to drive cutting heads, maneuver heavy loads, and ensure smooth operation in even the harshest conditions. The hydraulic system in a roadheader consists of pumps, actuators, valves, and hydraulic cylinders, all working in sync to control various components of the machine. This includes not only the cutting action but also the positioning of the cutter head, steering, and stabilizing the machine in challenging environments.
In standard models, hydraulic systems are designed for general use. However, modern roadheaders operate in a variety of environments, from soft rock to the hardest minerals, and each setting presents unique challenges. This is where custom hydraulic solutions come into play.
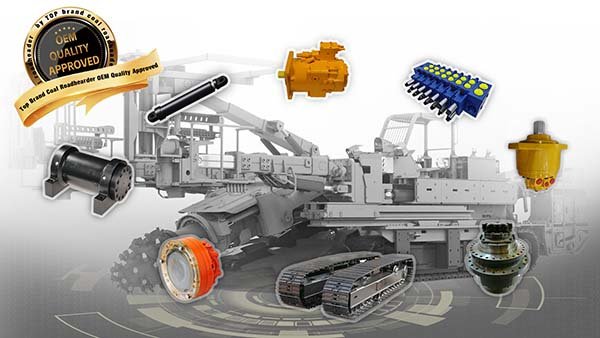
Why Custom Mobile Hydraulic Solution Matters?
Customization allows hydraulic systems to be fine-tuned for the specific needs of a project. Roadheaders are deployed in diverse applications such as mining, tunnel construction, and infrastructure development. Each project may have different requirements in terms of power output, mobility, and environmental considerations.
Enhanced Performance
Custom hydraulic solutions ensure that the roadheader performs optimally in specific conditions. For example, in hard rock mining, a more powerful hydraulic system may be needed to drive the cutter head through tough materials. In contrast, for softer materials, efficiency and speed may be prioritized over brute force.
Energy Efficiency
One of the key benefits of a custom hydraulic system is improved energy efficiency. Variable displacement pumps, for example, can be adjusted to deliver only the amount of power needed at any given time. This not only reduces fuel consumption but also minimizes wear and tear on the machine, extending its lifespan and reducing maintenance costs.
Adaptability to Environmental Conditions
Custom solutions can be designed to handle the specific environmental challenges that a roadheader may face. This includes high humidity, temperature extremes, or abrasive materials that can cause rapid wear on standard hydraulic components. Special seals, filtration systems, and corrosion-resistant materials can be integrated into the hydraulic system to ensure long-term reliability.
Precision Control
Tunneling and mining projects often require highly precise control over the roadheader’s cutting and positioning systems. Custom hydraulic actuators can be designed to provide this level of precision, allowing for smoother, more controlled movements that reduce the risk of damage to the surrounding rock or soil.
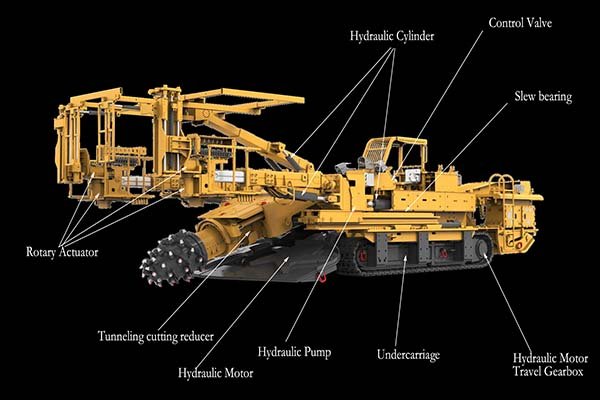
Key Components of a Custom Mobile Hydraulic Solution
Variable Displacement Pumps
Unlike fixed displacement pumps that deliver a constant flow, variable displacement pumps adjust the hydraulic output based on the demand of the system. This leads to greater efficiency and the ability to fine-tune the power delivered to the roadheader’s cutting head or positioning systems.
Hydraulic Actuators
Actuators control the movement of various components, from cutter head orientation to boom positioning. Custom actuators can be designed with specialized feedback mechanisms to ensure precise control, even in confined underground spaces.
Advanced Valves and Controls
Custom hydraulic systems often include sophisticated valve assemblies and electronic control systems that allow operators to adjust the machine’s behavior in real time. These controls can be programmed to optimize performance under varying conditions, making it easier to achieve consistent results.
Specialized Hydraulic Cylinders
In a roadheader, the hydraulic cylinders are responsible for controlling the movement of the cutting head and other critical components. Custom cylinders may feature heavy-duty construction, special coatings to reduce friction, and advanced sealing technologies to prevent fluid leaks.
The Future of Roadheader Technology
As industries continue to demand more from their excavation equipment, the importance of customization will only grow. Modern roadheader projects are more complex, often taking place in deeper, harsher environments. With the integration of smart technologies like remote monitoring and predictive maintenance, custom hydraulic systems will play a pivotal role in ensuring that roadheaders remain versatile and reliable.
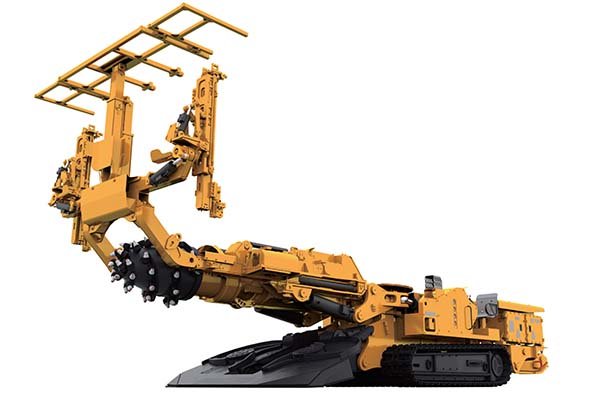
Conclusion
Custom mobile hydraulic solutions for modern roadheaders are essential for maximizing performance, improving energy efficiency, and ensuring precise control in challenging environments. By tailoring the hydraulic system to the specific needs of a project, manufacturers and operators can ensure that their roadheaders deliver optimal results. As the demands of underground mining and tunneling evolve, so too will the hydraulic technologies that power these indispensable machines.
Whether you’re working in the depths of a mine or cutting through dense urban infrastructure, a custom hydraulic system can make all the difference in the success of your project.