Hydraulic rotary actuators are essential in various industries, providing controlled rotational motion. Among them, the 180 degree hydraulic rotary actuators are particularly notable for their ability to deliver precise half-turn rotations.
How 180 Degree Hydraulic Rotary Actuators Work?
1. Basic Components
A typical 180 degree hydraulic rotary actuator consists of several key components: a hydraulic cylinder, a vane or piston mechanism, a housing, and a set of seals and bearings. The design may vary slightly depending on the specific application and manufacturer.
2. Hydraulic Power
Hydraulic fluid is the driving force behind these actuators. The fluid is pumped under pressure into the actuator, generating force that moves the internal components. The pressure and flow rate can be adjusted to control the speed and torque of the actuator’s movement.
3. Rotational Motion
In a vane-type actuator, the hydraulic fluid enters the chamber and pushes against a vane attached to a central shaft. As the vane rotates, it turns the shaft, converting the linear force of the hydraulic fluid into rotational motion. This rotation is precisely controlled, often limited to 180 degrees for specific applications.
4. Control and Feedback
Advanced models include sensors and control systems that monitor the position and performance of the actuator. These systems provide feedback to ensure accurate positioning and enable precise control of the rotational motion.
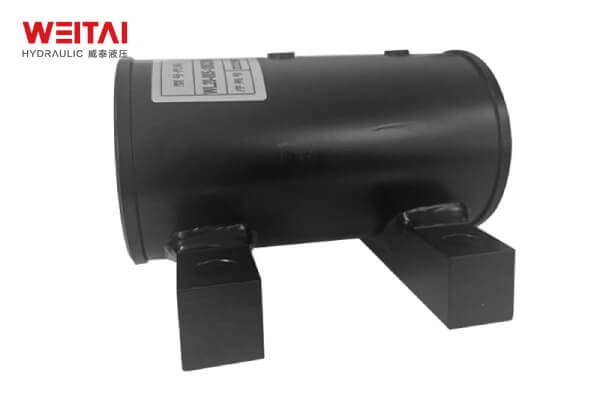
Key Benefits of Using 180 Degree Hydraulic Rotary Actuators
180-degree hydraulic rotary actuators are a popular choice for many automation applications due to their unique characteristics and capabilities. Here are some key benefits of using these actuators in industrial automation.
1. Precise and Controlled Motion
180-degree hydraulic rotary actuators offer precise control over rotational movement, making them ideal for applications requiring accurate positioning. The ability to precisely control the angle and speed of rotation ensures consistent and repeatable operations, essential for tasks like positioning workpieces, operating valves, and controlling robotic arms.
2. High Torque Output
One of the standout features of hydraulic rotary actuators is their ability to deliver high torque. This makes them suitable for heavy-duty applications where substantial force is required to move or hold loads. The high torque output enables efficient handling of large and heavy components, improving overall system performance.
3. Compact and Space-Saving Design
Hydraulic rotary actuators are compact and can deliver high power density, making them suitable for installations where space is limited. Their compact design allows for easy integration into various automation systems without requiring extensive modifications to existing setups.
4. Durability and Reliability
Built to withstand harsh industrial environments, hydraulic rotary actuators are known for their durability and long service life. They are resistant to dust, moisture, and temperature extremes, making them reliable even in challenging conditions. This reliability reduces maintenance needs and minimizes downtime, ensuring continuous operation.
5. Versatility in Applications
The ability to provide controlled 180 degree rotation makes these actuators versatile in various applications. They are used in material handling, assembly lines, packaging machinery, and more. Their adaptability allows them to be customized for specific tasks, making them a valuable component in diverse automation systems.
6. Energy Efficiency
Modern hydraulic rotary actuators are designed to be energy-efficient. Advanced hydraulic systems can regulate fluid flow and pressure, optimizing energy consumption and reducing operational costs. Energy efficiency is particularly beneficial in automation, where continuous operation can lead to significant energy savings.
7. Smooth and Quiet Operation
Hydraulic systems provide smooth and quiet operation, which is advantageous in environments where noise reduction is essential. The smooth motion also contributes to the precision and accuracy of the actuator’s performance, ensuring high-quality results in automation processes.
8. Easy Integration with Control Systems
180 degree hydraulic rotary actuators can be easily integrated with electronic control systems, including PLCs and CNC systems. This integration allows for advanced control features, such as programmable positioning, speed control, and feedback monitoring, enhancing the overall automation system’s flexibility and functionality.
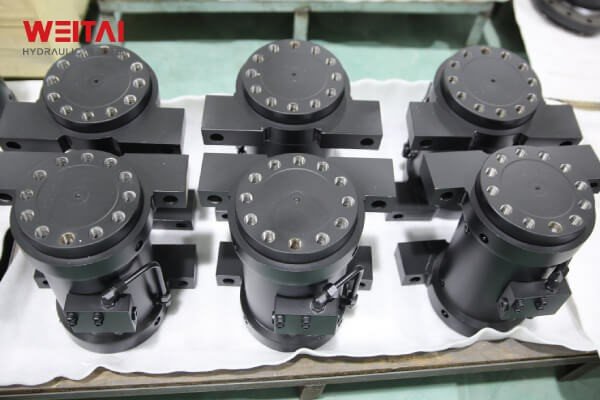
Where 180 Degree Hydraulic Rotary Actuators Are Used?
1. Industrial Automation
In manufacturing and automation, these actuators are used for tasks requiring precise positioning and rotation, such as opening and closing valves, positioning workpieces, and controlling robotic arms.
2. Construction Equipment
Hydraulic rotary actuators are integral to construction machinery like excavators and cranes, where they control the movement of booms, buckets, and other attachments.
3. Marine Applications
In the marine industry, these actuators are employed in systems like steering mechanisms, stabilizers, and hatch covers, where robust and reliable motion control is essential.
4. Aerospace and Defense
The aerospace and defense sectors use 180 degree hydraulic rotary actuators for various applications, including control surfaces, landing gear systems, and weaponry. The actuators provide the precision and reliability needed in these critical environments.
5. Renewable Energy
In the renewable energy sector, particularly in wind turbines, these actuators help adjust the pitch of the blades to optimize energy capture and protect the turbine from high wind speeds.
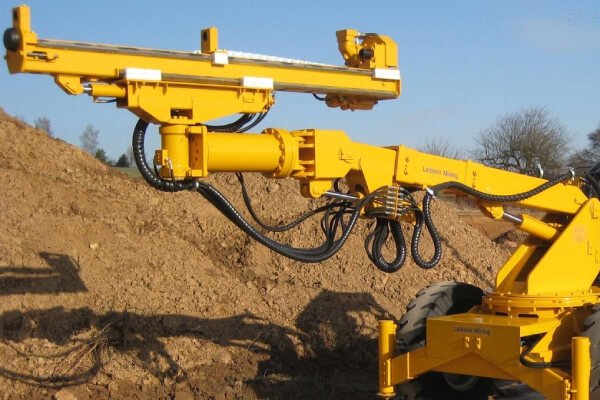
What’s New in 2024?
The world of hydraulic rotary actuators is constantly evolving, with new advancements enhancing performance, efficiency, and versatility. In 2024, the 180 degree hydraulic rotary actuator technology has seen several exciting innovations.
1. Advanced Materials and Lightweight Design
One of the significant trends in 2024 is using advanced materials to improve actuator performance and reduce weight. New composite materials and high-strength alloys offer enhanced durability while minimizing weight, leading to easier installation and lower energy consumption.
2. Smart Sensors and IoT Integration
Smart sensors have become integral to hydraulic systems, providing real-time data on actuator performance, including position, speed, and pressure. Integrating the Internet of Things (IoT) enables remote monitoring and predictive maintenance, reducing downtime and optimizing system efficiency.
3. Improved Seal Technologies
Seal technology advancements have significantly improved the reliability and lifespan of 180 degree hydraulic rotary actuators. New seal designs provide better resistance to wear, temperature fluctuations, and contamination, ensuring consistent performance even in harsh environments.
4. Energy-Efficient Designs
With a growing emphasis on sustainability, manufacturers have developed more energy-efficient hydraulic rotary actuators. Innovations include variable displacement pumps, energy recovery systems, and optimized hydraulic circuits that reduce energy consumption and operational costs.
5. Enhanced Control Systems
The latest control systems offer precise and responsive control of 180 degree rotary actuators. Advanced electronic controls and software algorithms provide smoother motion, increased accuracy, and customization options for specific applications.
6. Modular and Customizable Solutions
To meet diverse industry needs, manufacturers are offering modular and customizable actuator solutions. This approach allows for easy scalability, quick adaptation to different requirements, and simplified maintenance.
7. Integration with Collaborative Robots (Cobots)
As collaborative robots (cobots) become more prevalent in manufacturing and automation, 180 degree hydraulic rotary actuators are increasingly designed for seamless integration. These actuators are engineered to work safely alongside human operators, enhancing productivity and flexibility.
Conclusion
180 degree hydraulic rotary actuators are versatile devices that convert hydraulic energy into controlled rotational motion. Their robust construction and precise control make them indispensable in various industries, from automation and construction to aerospace and renewable energy.