A heavy equipment final drive is a crucial component within the powertrain system of various types of heavy machinery, such as excavators, bulldozers, loaders, and more. Its primary function is to transmit power from the engine to the tracks (in crawler-type equipment) or wheels (in wheeled equipment) of the machine.
Functionality
Power Transmission Efficiency: Final drives play a pivotal role in converting the high-speed, low-torque output generated by the engine into the slower-speed, higher-torque force required to drive heavy equipment. This transformation is crucial for maximizing operational efficiency and ensuring the equipment can effectively perform tasks such as excavation, grading, and material handling.
Gear Reduction Mechanism: Within the final drive assembly, a complex system of gears—typically including planetary gears—facilitates gear reduction. This process involves transmitting power through stages of gears to achieve the desired torque output suitable for the equipment’s operational needs. Gear reduction not only increases torque but also decreases rotational speed, aligning the output with the equipment’s optimal operational parameters.
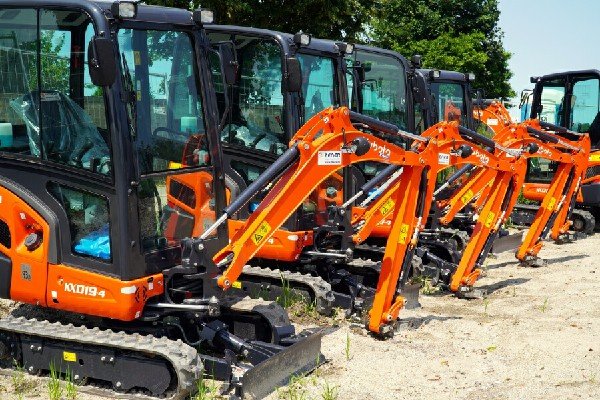
Components
Housing: The final drive assembly is enclosed within a robust housing structure, which serves multiple purposes. It provides protection against external elements such as dirt, debris, and moisture, safeguarding the internal gears, bearings, and seals from premature wear and damage. The housing also helps maintain the integrity of the lubrication system by preventing leaks and maintaining consistent lubricant levels.
Gears: Key components within the final drive assembly include the pinion gear, ring gear, and planetary gears. These gears work together to transmit and adjust the rotational force generated by the engine, effectively converting high-speed input into lower-speed output with increased torque. The arrangement of planetary gears allows for compact and efficient gear reduction, essential for heavy-duty applications where power and precision are paramount.
Bearings: Bearings within the final drive assembly provide critical support by enabling smooth rotation of gears and shafts. These bearings are designed to withstand heavy loads and continuous operation, ensuring minimal friction and optimal efficiency. Proper lubrication and maintenance of bearings are essential to prevent premature wear and maintain reliable performance over the equipment’s lifespan.
Seals: Seals are integral components that prevent leakage of lubricants and contaminants into the final drive assembly. They create a barrier between the internal components and external elements, maintaining the cleanliness and functionality of the lubrication system. High-quality seals are essential for extending the service life of the final drive by minimizing the risk of lubricant loss and component damage.
Lubrication System: The lubrication system of the final drive assembly ensures proper lubrication of gears, bearings, and seals. Adequate lubrication reduces frictional heat and wear, thereby enhancing the overall efficiency and durability of the equipment. Regular monitoring and maintenance of the lubrication system—including oil changes and inspections—helps prevent overheating, component failure, and costly repairs.
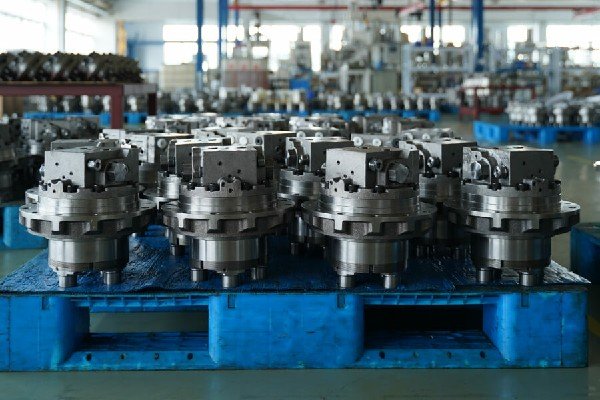
Importance
Enhanced Operational Efficiency: Efficient final drives are instrumental in optimizing the performance and productivity of heavy equipment. By transmitting power effectively and maintaining consistent torque output, well-maintained final drives enable operators to achieve greater operational efficiency and accomplish tasks with precision and reliability.
Durability and Reliability: Designed to withstand rigorous operating conditions and heavy workloads, final drives are engineered for durability and long-term reliability. Their robust construction and high-quality materials ensure resilience against impacts, vibrations, and environmental factors encountered in construction, mining, and other industrial applications.
Maintenance and Longevity: Proper maintenance of final drives is essential for maximizing equipment uptime and longevity. Routine inspections, lubrication, and timely replacement of wear components contribute to extended service life and reduced operating costs. Proactive maintenance practices also mitigate the risk of unexpected failures, minimizing downtime and ensuring continuous equipment availability on job sites.
Types
Crawler-Type Equipment: Final drives in crawler equipment are specifically designed to drive the tracks, providing traction, stability, and maneuverability across diverse terrain types. The final drives in crawler machines play a pivotal role in distributing power evenly to each track, enabling smooth movement and precise control during operations such as excavation, trenching, and earthmoving.
Wheeled Equipment: In wheeled equipment, final drives transmit power to the wheels, facilitating mobility and agility on various surfaces. Final drives in wheeled machines contribute to efficient steering, acceleration, and braking, enhancing the equipment’s versatility and performance in applications such as road construction, material handling, and transportation.
Maintenance Tips
1. Regular Inspections
Visual Inspection: Conduct regular visual inspections of the final drives for signs of leaks, damage, or excessive wear.
Check Fluid Levels: Monitor fluid levels (such as gear oil) in the final drives according to manufacturer specifications. Top up or change fluids as needed.
Inspect Seals and Bearings: Check seals and bearings for signs of wear or damage. Replace worn seals promptly to prevent contamination and subsequent damage.
2. Lubrication
Follow Manufacturer Guidelines: Use the recommended lubricants and follow the specified intervals for lubrication maintenance.
Ensure Proper Greasing: Grease fittings should be lubricated according to the equipment’s maintenance schedule to prevent premature wear and ensure smooth operation.
3. Cleaning
Keep External Surfaces Clean: Regularly clean external surfaces of the final drives to prevent buildup of dirt, debris, and contaminants that can lead to accelerated wear.
Inspect Ventilation: Ensure vents and breathers are clean and functioning properly to maintain proper pressure and prevent moisture ingress.
4. Monitoring Performance
Listen for Unusual Noises: Pay attention to any unusual noises coming from the final drives during operation, as they can indicate potential issues that need attention.
Monitor Performance Metrics: Use telematics or onboard monitoring systems, if available, to track operating temperatures and other performance metrics that could indicate problems.
5. Preventive Maintenance
Schedule Regular Servicing: Establish a proactive maintenance schedule based on manufacturer recommendations and operational conditions.
Replace Wear Parts: Replace worn-out components, such as gears, bearings, and seals, before they cause more significant damage to the final drives or other parts of the equipment.
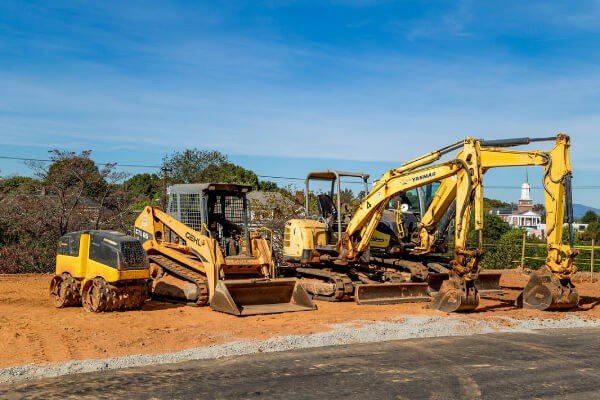
Conclusion
In summary, heavy equipment final drives are essential components that facilitate efficient power transmission, enhance operational performance, and ensure durability in demanding industrial environments. Understanding their functionality, components, and maintenance requirements is critical for optimizing equipment efficiency, reducing operational downtime, and maximizing return on investment in heavy machinery.